Van der Poorten
We make paper talk
Thanks to MultiPress, Van der Poorten never experiences press downtime due to stock issues
Since 1949, Van der Poorten Printing has been synonymous with quality and craftsmanship in the Belgian graphic industry. In 2017, they opted for MultiPress, Dataline’s advanced MIS/ERP system, marking a significant advancement in their workflow, with automation and flexibility as central features. In this interview, Jeroen and Dirk Van der Poorten share their experiences with MultiPress and the benefits it offers, from time savings to reduced errors.
From custom software to a complete solution
Van der Poorten had been using custom-built software for administration since 1985. However, over time, it became clear that this system had its limitations. “There were many manual tasks, such as retyping data, and the CRM structure was limited,” the Van der Poorten team explains. Switching to MultiPress provided the solution they needed: a flexible, fully integrated system tailored to meet the specific needs of the printing business. Key to their decision was not only the price and flexibility but also the positive experiences of other MultiPress clients in the Belgian print industry, including Die Keure, GSI, Burocad, and Hendrix.
The relationship between Dataline and Van der Poorten has been marked by a gradual implementation of MultiPress, with adjustments and solutions evolving alongside the company to align the system perfectly with their operations. The result is an efficient, sustainable solution that enables Van der Poorten to serve its clients better while streamlining internal processes.
One automated process
For Van der Poorten, MultiPress has automated the entire workflow, from estimation to invoicing, specifically tailored to their print production flow.
One of the major advantages of MultiPress for Van der Poorten is the Calculation Wizard, a crucial tool in their quotation process. “With the Calculation Wizard, we can quickly calculate standard products and generate an accurate quote within just a few clicks,” explains the team. This not only simplifies the quoting process but also speeds it up significantly, saving valuable time. In an industry where speed and accuracy are essential, this provides real added value.
Thanks to this integrated system, orders move seamlessly from quote to order confirmation and then to invoicing, all without additional steps. “MultiPress scheduling also gives us full control over the production process, allowing us to track and manage each stage as needed,” the team adds. This automation not only saves time but also minimises the risk of errors.
Seamless integration with Heidelberg via the JDF Link
For Van der Poorten, the ability to integrate with their Heidelberg machines through a JDF link was a significant advantage. The link ensures information is transferred directly and accurately to Heidelberg’s Prinect system. This makes the production process more efficient and minimises potential workflow bottlenecks. “We can now quickly and accurately send information to the machines, which greatly facilitates our production,” the team shares.
Inventory management in two clicks
Another strong point of MultiPress that Van der Poorten appreciates is the user-friendly inventory management. “I check the stock daily, and with just two clicks, I can see the current and minimum stock levels,” says owner Jeroen Van der Poorten. “This way, we can easily check if there’s enough paper on hand and reorder as needed, so we never run out.” This prevents delays in the production process and ensures deadlines are always met.
With Dataline’s MultiPress, Van der Poorten Printing has found a reliable ERP partner that contributes to a future-proof and efficient business operation!
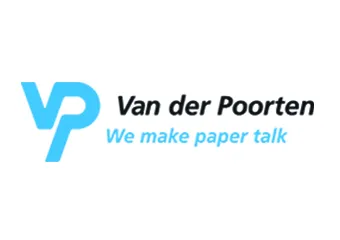
Company details
Van der Poorten Printing started in 1949 in a basement with a single hand press, but has since grown into a major player in the graphic sector. With over 45 employees and an impressive array of machinery, they are the go-to for books, magazines, leaflets, brochures, or annual reports.