5 signs that now is the time for automated print planning
27 August 2024
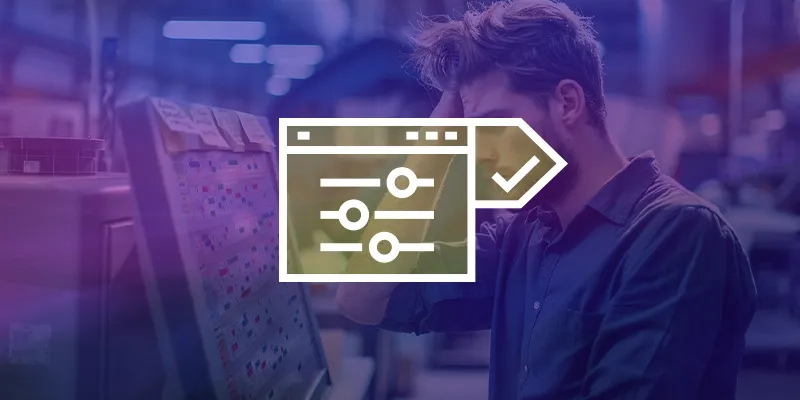
Have you ever felt that your planning is out of control? One order doesn't make it out the door on time because that one machine is overloaded, another is dragging on due to a miscommunication on the production floor. You're constantly behind schedule and struggling to get everything finished on time. What signs indicate that you need to automate your sign and print business planning? And most importantly, what does it bring to your business?
1. You have increasing numbers of small orders
Many sign and print businesses today receive a large number of small but urgent orders. For large orders, scheduling is actually relatively easy, but with an abundance of small orders, it becomes a challenge: you have to check whether you can save machine time by combining orders, ensure that the different stages of each order can follow each other smoothly and, above all, ensure that every machine in your machinery is used as optimally as possible.
On top of that, the administration is a lot more complex, because with traditional planning methods it is often not clear which orders have been processed each day and whether, for example, mistakes have been made that shrink profit margins. In short, this creates problems both internally and externally that you would prefer to avoid: you want satisfied customers because a satisfied customer is more loyal.
This is where an MIS/ERP software such as MultiPress comes in handy. For customers who place their print jobs in your stock, call-off orders allow you to keep track of your stock per customer, avoid unexpected shortages and avoid costly rush productions. This reduces the chance of surprises.
2. Project execution is delayed
Every graphics company faces projects that are delayed or even shut down from time to time. This can cause a lot of delays to creep into project execution, for instance:
- Production staff need to switch quickly due to a rush order.
- A machine not being adequately utilised because an administrative or prepress employee's schedule is overcrowded.
- An inefficient project execution when similar projects are not sequentially scheduled on the same machine.
So you always have to watch over the correct deployment of man and machine, something that goes more smoothly with a centralised database of an MIS/ERP software. Both administrative staff and people on the production floor get to see the same planning, which can easily be adjusted digitally and this way every team has the most recent planning available.
3. Cost estimates are done inaccurately
When cost estimates turn out to be inaccurate, it leads to budget overruns, a nightmare for any business. This can then lead to:
- Unexpected losses and pressure on profit margins.
- Dissatisfaction with your customer.
- Challenges in managing resources.
- Changes in project requirements.
You can actually avoid this problem quite easily with the right tools. MultiPress's calculation engine guarantees accurate price calculations, regardless of the type of print job or machine. This not only provides you with correct quotations with an appropriate sales price, but also gives you a direct view of the real production costs, production time and planning. Not only do you get an overview of all costs, but you also optimise your profit margins.
And you do not have to worry about the relationship of trust with your customers: your communication is clear from the first contact. In addition, any adjustments can easily be tracked.
4. There is a lack of overview and integration between departments
Inefficient order management, inventory management or production control creates numerous problems. You lose the overview and make mistakes or do unnecessary administration. Communication errors between administration and production lead not only to delays, but also to extra costs. Just think of printing errors, with costs going to extra ink, substrates and paper for a reprint. So smooth communication between departments is vital for a company that wants to operate seamlessly.
With the help of an MIS/ERP software such as MultiPress, it is possible to always be up-to-date with the necessary information.
- Good order management ensures that you never lose track. No more stress about the status of stock and/or materials being ordered on time. MultiPress collects all data, giving you an up-to-date overview of all orders and their status. Where necessary, you can intervene directly and make adjustments to monitor progress.
- In addition, stock management allows you to reserve materials for an order or effortlessly order a new load from your suppliers. This guarantees optimum use of your production capacity and on-time delivery of every order.
- And let's talk about accuracy. MultiPress registers all status updates and production data down to the smallest detail. No more guesswork, but detailed insight into every step of the process. For each order, you know which machines were used, what the production time was and whether any errors occurred.
Documents and processes are so much easier to follow up in every department.
5. There is a high administrative workload
An abundance of administrative tasks has a negative impact on efficiency and costs within your company. Just consider that 40% of a product order consists of administrative costs, mainly due to high labour costs.
Moreover, with 40% of administrative costs, it becomes a challenge to offer competitive rates and maintain a decent profit. MultiPress removes the burden of manual administrative tasks and costs and streamlines workflows. This allows the team to focus on the more important aspects of their job.
Just like 3motion, L'Arts and Mediacenter Rotterdam, optimise your planning!